在实际操作中,FMEA分为设计FMEA(DFMEA)和过程FMEA(PFMEA)两大类。设计FMEA侧重于产品设计阶段,关注产品功能和设计特性可能引发的失效及其对用户的影响;而过程FMEA则聚焦于生产制造过程,分析各工序中潜在的失效模式及其对产品质量、成本和生产效率的影响。两者相辅相成,共同构成了从产品设计到生产实现的全链条风险管理框架。执行FMEA时,团队成员需运用专业知识和实践经验,对每一个潜在失效模式进行量化评估,如严重度(S)、发生频度(O)、探测度(D),并计算风险优先数(RPN),以此为依据确定改进措施的优先级。这一过程不仅促进了团队间的沟通与协作,还为企业积累了宝贵的知识资产,为后续的产品开发和过程优化提供了坚实的数据支持。FMEA强调风险管理的重要性。浙江运输车制造失效分析降低质量成本
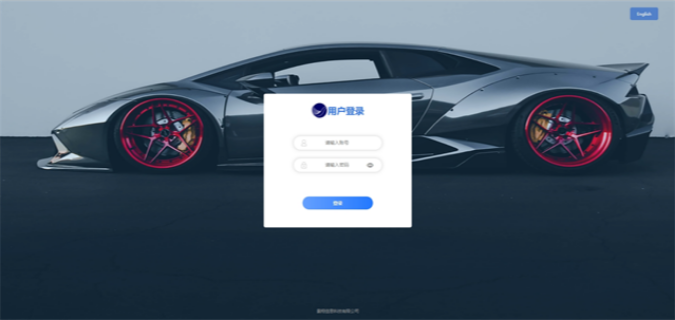
在医院的日常运营中,风险无处不在,而 FMEA 为医院相关企业带来了全新的风险管理思路。FMEA 可以对医疗设备的维护和管理进行分析,预测可能出现的故障模式,如设备突然停机、精度下降等。通过提前采取预防措施,如定期保养、备件储备等,降低了设备故障对医疗服务的影响。某医疗器械维修企业,运用 FMEA 对医院设备进行风险评估,为医院提供了个性化的维护方案,提高了设备的可靠性和使用寿命。让 FMEA 成为您企业与医院合作的桥梁,共同为医疗服务的安全高效贡献力量。浙江运输车制造失效分析降低质量成本FMEA让企业更加关注风险识别。
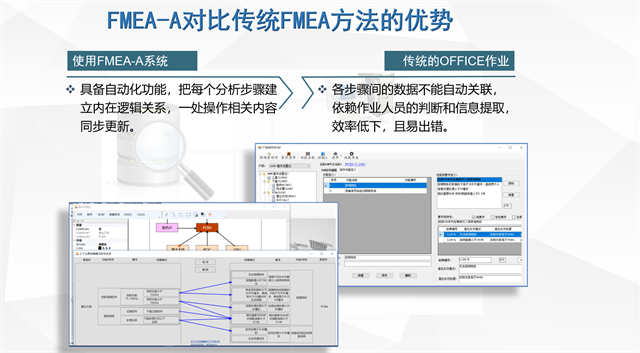
产品失效模式分析是质量管理和可靠性工程中至关重要的环节,它通过对产品或系统在使用过程中可能出现的失效形式进行全方面、系统的研究,旨在预防或较小化这些失效的发生。这一分析过程通常涉及识别潜在的失效原因、评估失效对产品和系统性能的影响程度,以及制定针对性的纠正措施和预防措施。在进行产品失效模式分析时,工程师们会运用各种工具和技术,如故障树分析、失效模式与影响分析(FMEA)等,来深入剖析每个潜在失效模式的根本原因,并量化其可能导致的风险。通过综合考虑设计、制造、使用和维护等多个阶段的因素,产品失效模式分析有助于提升产品的整体质量和可靠性,减少维修成本,延长产品寿命,增强客户满意度和市场竞争力。
潜在失效模式与后果分析(FMEA)是一种系统化的方法,普遍应用于产品设计、制造过程以及服务流程中,旨在识别、评估并预防潜在的失效及其可能带来的后果。这一方法通过组建跨职能团队,汇集来自设计、制造、质量控制等不同领域的专业知识,共同对产品或过程的每一个步骤进行深入分析。它要求团队成员不仅考虑直接的失效原因,还要分析那些可能看似不相关但实际上能引发连锁反应的因素。在识别出潜在的失效模式后,FMEA进一步评估这些失效模式的严重度、发生频度和探测度,从而计算出风险优先数(RPN),帮助决策者识别出哪些问题需要优先解决。这一过程不仅提升了产品或服务的质量,还明显降低了后期更改的成本,增强了企业的市场竞争力。FMEA为企业提供了一种长效的风险管理机制。
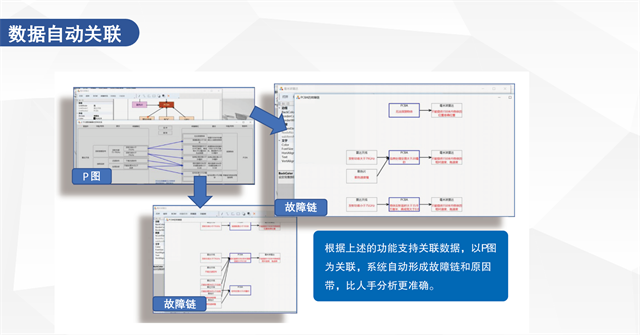
FMEA表格的应用不仅限于产品设计阶段,它也贯穿于整个产品生命周期,包括生产准备、过程控制和持续改进等环节。在生产准备阶段,通过FMEA表格可以识别出生产线上的潜在问题点,提前做好预防措施,如优化工艺参数、增加检测设备或改进工装夹具等,以减少生产过程中的质量波动。在过程控制阶段,FMEA表格作为监控和评估工具,能够及时发现和纠正过程中的偏差,防止不良品流入下一道工序。定期的FMEA回顾和更新,有助于团队持续挖掘潜在的改进机会,推动产品和过程的不断优化。通过充分利用FMEA表格,企业能够建立起一套科学的风险管理体系,确保产品质量的持续改进和稳步提升。FMEA让企业更加关注风险评价。江西影视器材制造失效分析零缺陷管理
引入FMEA,企业创新能力得到加强。浙江运输车制造失效分析降低质量成本
在实际应用中,失效模式及影响分析不仅是一种技术工具,更是一种管理理念和持续改进的文化。它鼓励跨部门协作,促进知识共享,使得从设计到生产的每一个环节都能深刻理解各自责任范围内的潜在风险。通过定期回顾和更新FMEA文档,企业能够紧跟技术发展和市场需求的变化,灵活调整应对策略。FMEA还有助于培养员工的预见性思维,提升问题解决能力,确保在面对未知挑战时,团队能够迅速响应,有效避免或减轻失效带来的负面影响。失效模式及影响分析是现代质量管理不可或缺的一部分,它为企业提供了从源头控制风险、实现持续改进的有效途径。浙江运输车制造失效分析降低质量成本
文章来源地址: http://swfw.nongyejgsb.chanpin818.com/jypxud/glpxxv/deta_27739074.html
免责声明: 本页面所展现的信息及其他相关推荐信息,均来源于其对应的用户,本网对此不承担任何保证责任。如涉及作品内容、 版权和其他问题,请及时与本网联系,我们将核实后进行删除,本网站对此声明具有最终解释权。