基于Q-TOP QMS系统的供应链质量协同管理体系 供应链质量协同是企业实现价值链优化的重要保障。Q-TOP QMS系统通过整合质量管理六大工具和PDCA循环管理,构建了贯穿供应链全流程的质量协同机制。 在Plan(计划)阶段,系统运用APQP工具制定供应链质量协同方案。某整车制造企业通过Q-TOP系统的APQP模块,与32家基本供应商建立统一的质量标准体系,来料合格率提升至99.2%。同时结合QFD将终端客户需求转化为供应链质量要求。 在Do(执行)阶段,系统集成SPC和供应链智能监控技术。某电子制造企业部署供应商质量看板后,异常响应速度提升60%。条码追溯技术的应用实现物料全生命周期质量数据可视化管理。 Check(检查)阶段,系统通过MSA确保供应链检测数据一致性。某装备制造企业将供应链测量系统差异控制在5%以内。系统自动生成供应商质量绩效报告,实现客观评价。 Act(改进)阶段,系统结合8D报告和联合改善工具。某医疗器械企业通过Q-TOP系统推动供应商实施15项质量改进措施,批次不合格率下降75%。同时建立供应商质量能力提升机制。 Q-TOP QMS系统还通过FMEA工具识别供应链质量风险。某食品企业应用后,原材料质量波动幅度缩小60%,产品稳定性明显提高。质量管理系统确保合规要求。连云港实施质量管理系统供应商
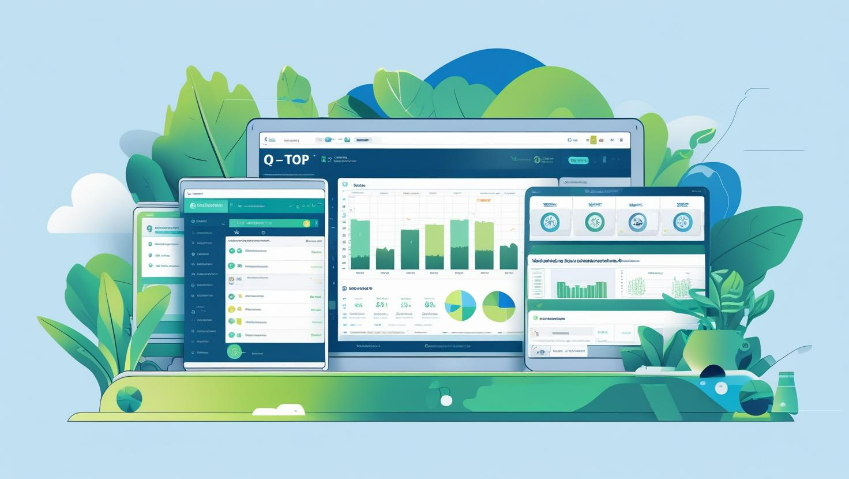
人为差错是制造过程中影响产品质量的重要因素。Q-TOP QMS系统通过整合质量管理六大工具和PDCA闭环管理,构建了系统化的人为差错防控体系,有效提升生产过程可靠性。 在Plan(计划)阶段,系统运用FMEA工具对关键工序进行失效模式分析。某电子制造企业通过Q-TOP系统的FMEA模块,识别出焊接工序的15个潜在人为失误点,并制定针对性防错措施。 在Do(执行)阶段,系统整合SPC和防错(Poka-Yoke)工具。实时监控关键参数的同时,在装配线设置智能检测工装。某汽车零部件企业应用后,操作失误导致的返工率从3.2%降至0.5%。 Check(检查)阶段,系统通过MSA(测量系统分析)确保检测可靠性。某 Act(改进)阶段,系统结合5Why分析和PDCA循环。 Q-TOP QMS系统还整合了控制计划(Control Plan)工具,将防错措施标准化。 该系统通过PDCA闭环管理,持续优化防错机制。未来,随着AI技术的深度融合,系统将实现更智能的人为差错预测与预防。南通实施质量管理系统价格质量管理系统优化生产流程。
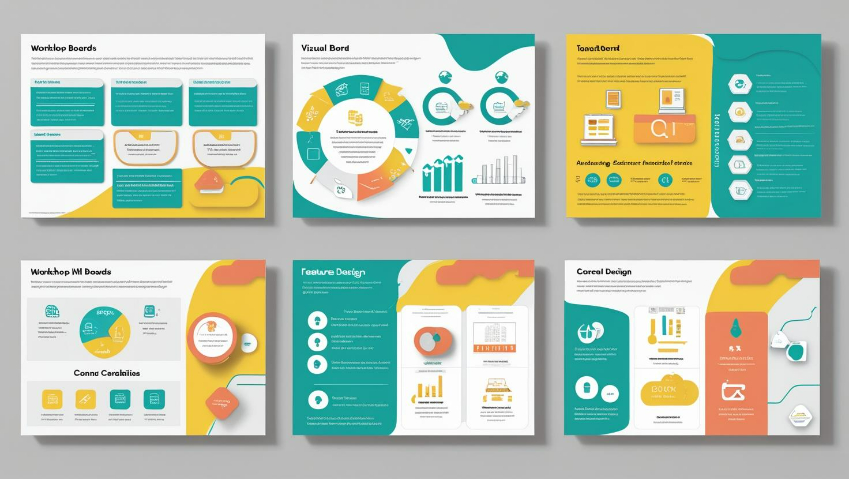
设备运行效率的优化是企业实现提质增效的重要途径。Q-TOP QMS系统通过整合质量管理六大工具和PDCA循环管理,构建了科学的设备效能提升机制。 在Plan(计划)阶段,系统运用FMEA工具识别设备效率瓶颈。某汽车制造企业通过Q-TOP系统的FMEA模块,发现并评估了8个关键效能影响因素,制定针对性改进方案。同时结合APQP制定设备效能提升路径。 在Do(执行)阶段,系统集成SPC和智能监测技术。某电子企业部署设备状态实时监控后,异常停机时间减少65%。自适应维护策略使设备综合效率(OEE)从75%提升至92%。 Check(检查)阶段,系统通过MSA确保设备数据准确性。 Act(改进)阶段,系统结合5Why分析和标准化工具。 Q-TOP QMS系统还通过防错技术预防设备操作失误。 该系统通过PDCA闭环管理,实现了设备效能的持续提升。随着工业物联网技术的应用,系统将为企业提供更准确的设备状态预测和更智能的维护决策支持。
基于Q-TOP QMS系统的跨部门协同管理体系 部门协作效率是企业质量管理效能的重要保障。Q-TOP QMS系统通过整合质量管理六大工具和PDCA循环管理,构建了高效的跨部门协同机制。 在Plan(计划)阶段,系统运用QFD工具统一部门目标。某制造企业通过Q-TOP系统的QFD模块,将客户需求转化为8个部门的28项协同指标,目标对齐度达97%。同时结合APQP制定协同实施方案。 在Do(执行)阶段,系统集成SPC和智能协同平台。某汽车企业部署实时数据共享后,部门响应时效提升65%。智能任务分配功能使流程衔接时间缩短50%。 Check(检查)阶段,系统通过MSA确保协同数据一致性。某电子企业将关键指标测量误差控制在3%以内。系统自动生成协同效能评估报告。 Act(改进)阶段,系统结合5Why分析和标准化工具。某制药企业通过Q-TOP系统优化协作流程后,信息传递效率提高40%。同时建立良好实践共享库。 Q-TOP QMS系统还通过防错技术预防协作失误。 该系统通过PDCA闭环管理,实现了协作效能的持续提升。随着数字孪生技术的应用,系统将为企业提供更直观的协同模拟和更准确的资源调配方案。质量管理系统培养质量意识。
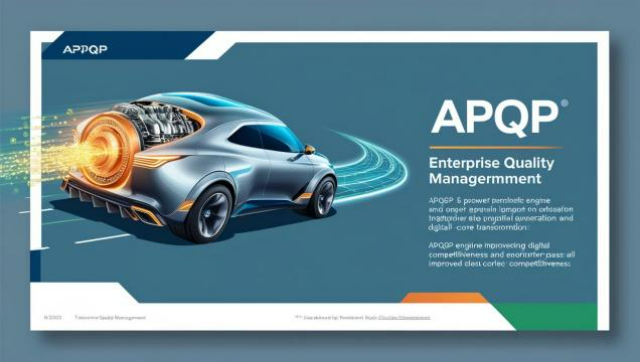
产品一致性是衡量制造水平的基本指标。Q-TOP QMS系统通过整合质量管理六大工具和PDCA循环管理,构建了全过程的一致性控制体系。 在Plan(计划)阶段,系统运用APQP工具制定一致性控制方案。某精密制造企业通过Q-TOP系统的APQP模块,对25个关键特性建立管控标准,工艺规范覆盖率提升至100%。同时结合FMEA分析潜在变异因素。 在Do(执行)阶段,系统集成SPC和自适应调节技术。某汽车零部件企业部署实时过程监控后,关键尺寸波动范围缩小60%。智能补偿系统使CPK值稳定在1.67以上。 Check(检查)阶段,系统通过MSA确保检测数据准确性。 Act(改进)阶段,系统结合5Why分析和标准化工具。 Q-TOP QMS系统还通过防错技术消除人为变异因素。 该系统通过PDCA闭环管理,实现了产品一致性的持续提升。随着智能制造技术的应用,系统将为企业提供更准确的过程调控和更稳定的质量输出。质量管理系统减少售后问题。马鞍山汽车电子质量管理系统价格
质量管理系统加强过程管控。连云港实施质量管理系统供应商
生产过程的稳定性是保证产品质量一致性的关键要素。Q-TOP QMS系统通过整合质量管理六大工具和PDCA循环管理,建立了多面的生产过程稳定控制体系。 在Plan(计划)阶段,系统运用APQP工具制定工艺稳定性方案。某精密制造企业通过Q-TOP系统的APQP模块,对28个关键工序进行工艺能力评估,制定针对性的稳定措施。同时结合FMEA分析潜在过程波动因素。 在Do(执行)阶段,系统集成SPC和智能调节技术。某汽车零部件企业部署实时过程监控后,关键参数CPK值从1.2提升至1.8。自适应控制技术的应用使工艺波动幅度缩小65%。 Check(检查)阶段,系统通过MSA确保过程监控数据的准确性。某电子企业将测量系统GR&R控制在5%以内系统自动生成过程稳定性分析报告,及时发现异常趋势。 Act(改进)阶段,系统结合5Why分析和标准化工具。 Q-TOP QMS系统还通过防错技术消除人为因素干扰。连云港实施质量管理系统供应商
文章来源地址: http://swfw.nongyejgsb.chanpin818.com/rjkf/deta_28734833.html
免责声明: 本页面所展现的信息及其他相关推荐信息,均来源于其对应的用户,本网对此不承担任何保证责任。如涉及作品内容、 版权和其他问题,请及时与本网联系,我们将核实后进行删除,本网站对此声明具有最终解释权。